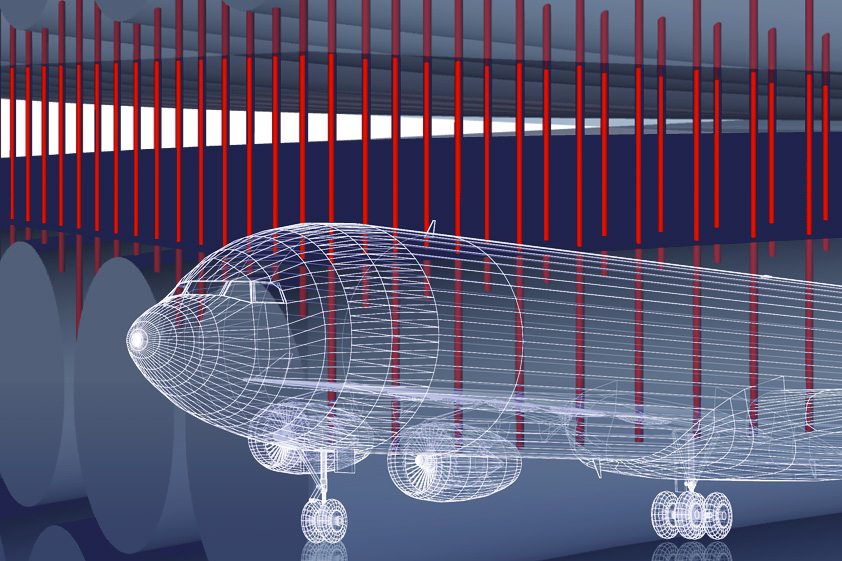
Today, the latest Airbus and Boeing passenger jets feature components made from advanced composite materials such as carbon fibre-reinforced plastic, which are extremely light and durable and can reduce the overall weight of an aeroplane by at least 20%, which saves on fuel.
Composite materials are made by combining two or more materials that each have significantly different physical or chemical properties. When added together, the material produced is stronger and features different characteristics to the individual component layers that went into it, and apart from plastic, this technique is routinely used to engineer stronger concrete, ceramics and metals.
However, when put under stringent conditions, not all composite materials are equally strong, so while aluminium can withstand a relatively large impact without cracking, the same cannot be said for a material like plastic.
Carbon nanotubes to the rescue
To solve this problem, MIT's aerospace engineers have experimented with using carbon nanotubes to stitch the layers of composite materials together, embedding tiny "forests" of carbon nanotubes within a sticky glue-like polymer matrix that is inserted between layers of carbon fibre composites.The researchers found that when they tested the new material's strength against that of existing carbon fibre reinforced plastic composites, the plastic material that had been stitched together was 30% stronger and could withstand much stronger forces without cracking.
"More work needs to be done, but we are really positive that this will lead to stronger, lighter planes," said Roberto Guzman, a postdoc in MIT's Department of Aeronautics and Astronautics (AeroAstro) who is now a researcher at the IMDEA Materials Institute in Spain.
If you were to use a nail or a stitch to bond the layers of a composite material like plastic together, because these tools are both thousands of times bigger than the carbon fibres, thousands of layers would be damaged if you were to drive the nail or the stitch into the material.
Reinforced materials can be safely used in aircraft
In contrast, carbon nanotubes are 10 nanometres in diameter, which is nearly a million times smaller than the carbon fibres, so instead of breaking the fibres, the nanotubes resemble vertically-aligned stitches like on a sewing machine which meld into the crevices of each layer to keep them together."The strength enhancements suggest this material will be more resistant to any type of damaging events or features," said Brian Wardle, an AeroAstro professor and Director of Necstlab and the Nano-engineered Composite Aerospace Structures Consortium.
"And since the majority of the newest planes are more than 50% composite by weight, improving these state-of-the art composites has very positive implications for aircraft structural performance."
So far, the aerospace industry has been wary of using carbon fibre reinforced plastic too widely due to the material strength concerns, but it is hoped that with the new technique, there will be more confidence to use these materials to build more parts of aircraft.
The research, entitled: "In-plane strength enhancement of laminated composites via aligned carbon nanotube interlaminar reinforcement" is published in the journal Composites Science and Technology.
0 Response to "MIT revolutionises aeroplane design with material-strengthening technique for carbon nanotubes"
Post a Comment